LPG & CNG Cylinder Production Lines
REPKON offers complete turnkey solutions for the LPG Cylinder Production (and Maintenance) Facilities to manufacture (or to perform overhaul maintenance of) the domestic, industrial and picnic type LPG cylinders through blanking and body forming line: welding, heat treatment & hydrostatic testing line: surface coating & finishing line.
LPG Cylinder Production within the guidelines of the international standards such as EN 1442 involves several process steps starting from forming to final testing that can be streamlined into the following lines:
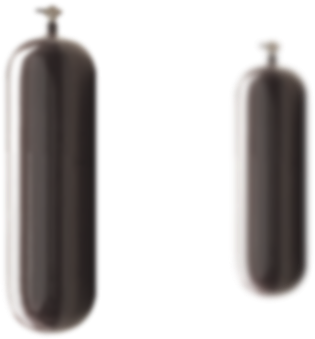
Blanking And Body Forming Line
In the core of the forming line there stands a versatile double action REPKON hydraulic deep drawing press that forms the cylinder halves out of round blanks that are blanked by a single action double blanking REPKON press or directly from the coil material by help of REPKON design combined deep drawing, piercing and blanking die set. The edges of the upper and lower halves are further processed by REPKON trimming and joggling machines to the perfection stemming from the sheet metal forming expertise of REPKON to make it read for the body seam welding after degreasing.
Welding, Heat Treatment & Hydrostatic Testing Line
The submerged arc welding technique is applied on the welding of body halves on the seam welding machine and generally on the wielding of the valve boss to the upper cylinder halve. The welding automats with reliable welding power packs and control units are utilized to achieve the uncompromising weld quality with degree of automation needed for the required production capacity per customer. The MIG/MAG welding technique is applied for the welding of foot rings and valve guard rings with the body halves.
In order to relive all the stresses caused by forming and welding operations, the cylinders are passed through a heat treatment furnace where they are exposed to 930 º C degrees of temperature for certain time before getting cooled gradually.
Surface Coating & Finishing Line
The LPG cylinders surfaces are shot blasted by the shot blasting machine in order to clean up the scales caused by the heat treatment operation to make the surface ready for the painting and or zinc spraying for those customers who requires zinc coating before painting. The double layer over cured painting of the cylinders is achieved automatically by the robotic paint application system in the painting line as the cylinders conveyed on overhead conveyor system through the primary and final coat painting cabinets separated by flash off tunnels before they get cured in the canopy type modern paint curing oven.
After the tare weighing and marking of the cylinders, the valves are attached by automatic torque controlled screwing machines and tested against any leakage at the valve region by the pneumatic leakage testing machine of the finishing line.
One of the batch type quality control equipment called by the international standards is the burst expansion testing unit where the volumetric expansion ratio and the burst pressure is measured to the full satisfaction of even most stringent requirements.
High Pressure Cylinders Production Plants
REPKON offers a wide range of engineering and manufacturing experience to its customers by establishing turnkey High Pressure Gas Tube production facilities in compliance with international standards such as ISO-11439, ISO-9809 or ECE-R-110. Depending on the volume of high-pressure tubing it can vary from a few liters to over 100 liters volume. High pressure tubing is used for many different functions, such as medical or industrial gas cylinders, battery cells, CNG containers for gas-powered vehicles or diving tubes. REPKON offers advanced and modern technology solutions for all high pressure cylinders in accordance with international quality standards. The production of high pressure tubes which can be made of seamless pipe, sheet or billet as starting material, involves different forming processes.
Hot Spinning Machines for Bottom Closing & Necking-in Operations
The REPKON RNM 41-120 Hot Spinning Machine is especially designed for the manufacturing of seamless CNG cylinders and other types of high pressure gas cylinders. The machine is used both for gas tight bottom closing and for necking in operations with proper tooling. The RNM 41-120 Hot Spinning Machine can be tooled to perform bottom closing or necking-in operations. Equipped with an integral induction heating furnace and automatic loading / unloading system to optimize operation efficiency in short cycle times, RNM Series ensure impeccable process quality by its unique designs.The induction heating furnace is part of REPKON RNM 41-120 machine and integrated in the machine structure. The tubes are heated up partially in the induction-furnace at forging temperature before loading to the machine. After heating, the work-piece is automatically carried to the main-spindle, loaded from the front and clamped from the outside. When the hot spinning operation finished, the work-piece is unloaded onto the rotary holder and with the rotation of it is unloaded onto the exit table while the new work-piece is being loaded into the chuck.